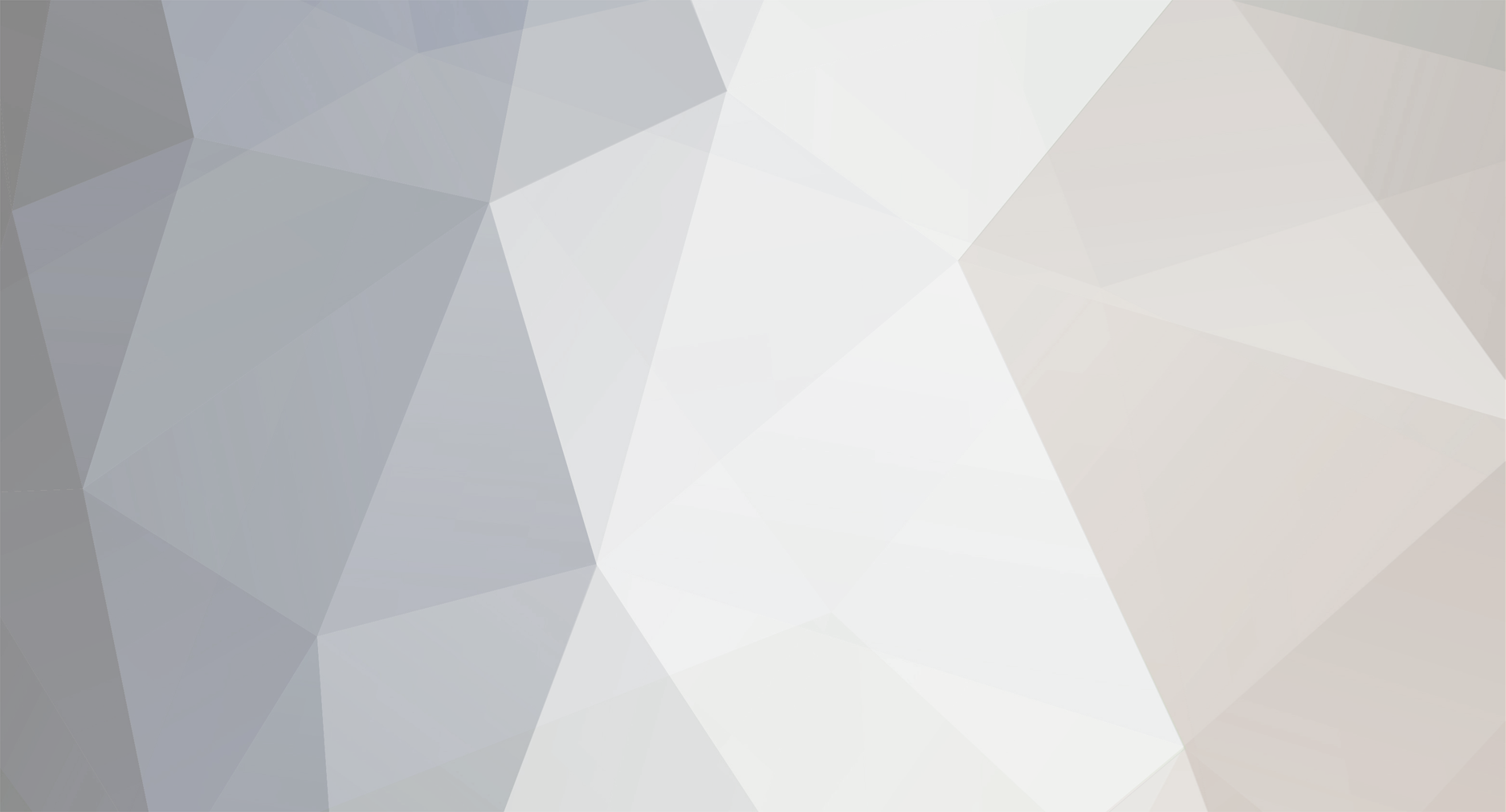
han_5583
-
Posts
4 -
Joined
-
Last visited
Never
Content Type
Profiles
Forums
Downloads
Gallery
Posts posted by han_5583
-
-
Hi All,
Currently I'm doing a project on RPM sensor connecting to Labview. My RPM sensor uses IR transmitter/receiver. When the motor turns in front of the IR transmitter receiver, the IR light will be reflected back and the circuit will have an increase of voltage from 1.8V to 3.2V. I'm planning to connect this output voltage to the Labview via the digital input, but I'm having problem as how to do the programming in Labview to calculate the rpm of the motor.
Appreciate if anybody can help me on this.
Thanks
Amy Tan
-
this was what i have done.
-
Hi guys, I'm a moderate labview user and I have done a few project before. My current project is about generating PWM signals to control the rpm of an electric motor. When I simulate the signal I can see the generated PWM clearly on the virtual graph, but when I connect it with the DAQ assistant (analog output), the PWM signals suddenly run very slow. I suspect I dont provide enough buffer to the output, but I dont know how to increase the buffer size. Currently the PWM signals does not go through the DAQ device. Anyway, I'm using USB-6008. Please advice.
rpm sensor
in Hardware
Posted
QUOTE (mross @ Jul 16 2008, 02:17 PM)
Hi Mike,
Thanks for your advice. Actually I do plan to use the analog voltage, but I'm not sure my DAQ (USB-6008) is a buffered DAQ. Do you have any example on how to use the input voltage for the counter? I was hoping to measure how many pulse within a minute but I'm not sure how to do that.
Thanks in advance