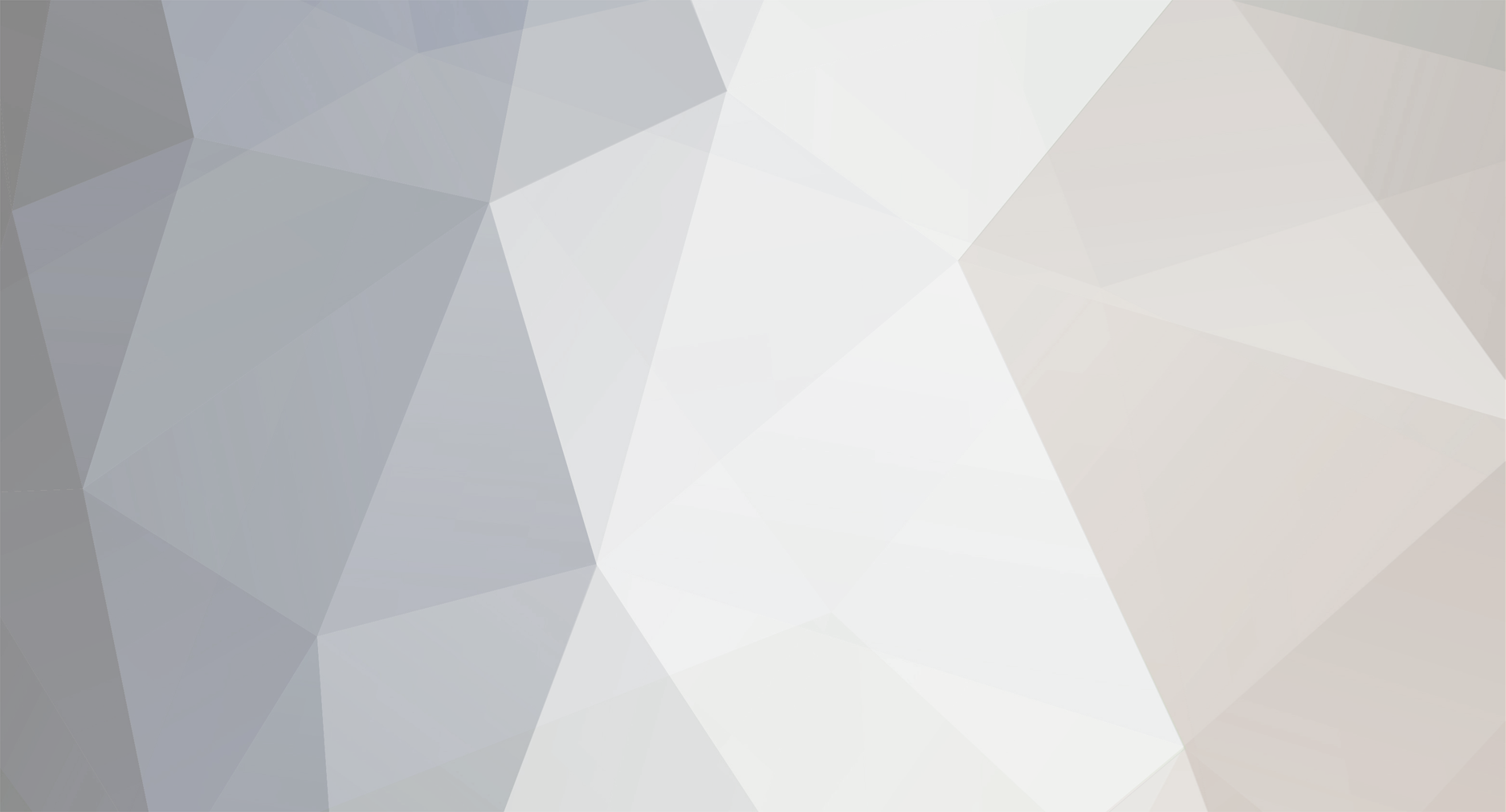
SasiU
-
Posts
3 -
Joined
-
Last visited
Never
Content Type
Profiles
Forums
Downloads
Gallery
Posts posted by SasiU
-
-
Hi,
My name is Sasi. I am a BME Grad student from Ohio. I am working to build a flexibility spine test machine towards my thesis topic which deals with evaluating implants using this machine. I have to write a LabVIEW code to control a brushless AC servo gearmotor using torque cell data as feedback. I have managed to get the hardware part right, i.e they r being identified and controlled. I have also written a very crude code to achieve the following.
Step 1: Initialize the motor.
Step 2: Start moving it at a uniform RPM to the right (This RPM value too user can enter).
Step 3: While doin Step 2; simultaneously read torque cell data (Using DAQ asst.). DAQ o/p is from 0 V to 10 V; 0 V being -10 Nm n
10 V being +10 Nm
Step 4: When Torque value reaches +10 Nm, i.e 10 V, the motor stops.
Step 5: From the position where motor stopped (i.e no need to reset to initial position) Start moving in the opposite direction at the same
uniform RPM as in Step 2 while reading torque cell data.
Step 6: Once again when torque reaches -10 Nm, i.e. 0 V, the motor should stop.
Step 7: Repeat 'Step 2' to 'Step 6' 3 times.
Step 8: Reset motor postion.
I have managed to get the forward n backward motion by loading +Vel n -Vel values to Read velocity.flx in trajectory settings, but I am having problem putting them in a case structure to do so when user clicks a toggle switch on front panel. Also Can anyone help me with a better logic, i.e including emergency stop, etc. cause it is having motor movement n etc. n u knw spine is usually very delicate, so if by mistake anyone enters huge values for vel, etc. it wud be bad. I really appreciate all you ppl's help.
PFA initial code file for your ref.
Thnks,
Sasi.
-
Hi,
My name is Sasi. I am a BME Grad student from Ohio. I am working to build a flexibility spine test machine towards my thesis topic which deals with evaluating implants using this machine. I have to write a LabVIEW code to control a brushless AC servo gearmotor using torque cell data as feedback. I have managed to get the hardware part right, i.e they r being identified and controlled. I have also written a very crude code to achieve the following.
Step 1: Initialize the motor.
Step 2: Start moving it at a uniform RPM to the right (This RPM value too user can enter).
Step 3: While doin Step 2; simultaneously read torque cell data (Using DAQ asst.). DAQ o/p is from 0 V to 10 V; 0 V being -10 Nm n
10 V being +10 Nm
Step 4: When Torque value reaches +10 Nm, i.e 10 V, the motor stops.
Step 5: From the position where motor stopped (i.e no need to reset to initial position) Start moving in the opposite direction at the same
uniform RPM as in Step 2 while reading torque cell data.
Step 6: Once again when torque reaches -10 Nm, i.e. 0 V, the motor should stop.
Step 7: Repeat 'Step 2' to 'Step 6' 3 times.
Step 8: Reset motor postion.
I have managed to get the forward n backward motion by loading +Vel n -Vel values to Read velocity.flx in trajectory settings, but I am having problem putting them in a case structure to do so when user clicks a toggle switch on front panel. Also Can anyone help me with a better logic, i.e including emergency stop, etc. cause it is having motor movement n etc. n u knw spine is usually very delicate, so if by mistake anyone enters huge values for vel, etc. it wud be bad. I really appreciate all you ppl's help.
PFA initial code file for your ref.
Thnks,
Sasi.
AC servo Motor control
in Hardware
Posted
Hi,
My name is Sasi. I am a BME Grad student from Ohio. I am working to build a flexibility spine test machine towards my thesis topic which deals with evaluating implants using this machine. I have to write a LabVIEW code to control a brushless AC servo gearmotor using torque cell data as feedback. I have managed to get the hardware part right, i.e they r being identified and controlled. I have also written a very crude code to achieve the following.
Step 1: Initialize the motor.
Step 2: Start moving it at a uniform RPM to the right (This RPM value too user can enter).
Step 3: While doin Step 2; simultaneously read torque cell data (Using DAQ asst.). DAQ o/p is from 0 V to 10 V; 0 V being -10 Nm n
10 V being +10 Nm
Step 4: When Torque value reaches +10 Nm, i.e 10 V, the motor stops.
Step 5: From the position where motor stopped (i.e no need to reset to initial position) Start moving in the opposite direction at the same
uniform RPM as in Step 2 while reading torque cell data.
Step 6: Once again when torque reaches -10 Nm, i.e. 0 V, the motor should stop.
Step 7: Repeat 'Step 2' to 'Step 6' 3 times.
Step 8: Reset motor postion.
I have managed to get the forward n backward motion by loading +Vel n -Vel values to Read velocity.flx in trajectory settings, but I am having problem putting them in a case structure to do so when user clicks a toggle switch on front panel. Also Can anyone help me with a better logic, i.e including emergency stop, etc. cause it is having motor movement n etc. n u knw spine is usually very delicate, so if by mistake anyone enters huge values for vel, etc. it wud be bad. I really appreciate all you ppl's help.
PFA initial code file for your ref.
Thnks,
Sasi.