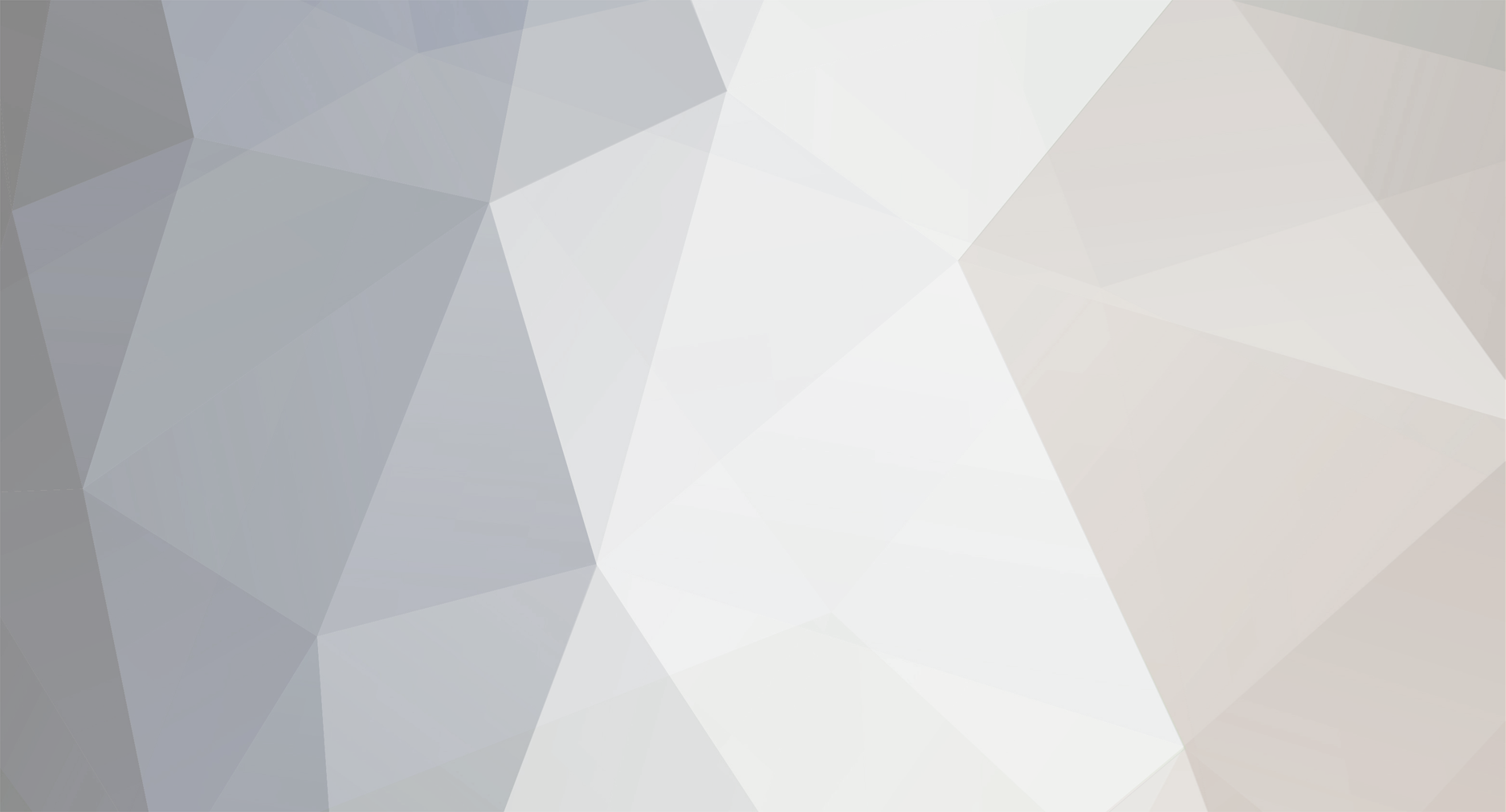
rrd
-
Posts
4 -
Joined
-
Last visited
Never
Content Type
Profiles
Forums
Downloads
Gallery
Posts posted by rrd
-
-
If the other channels are not connected to anything, their readings will tend to 'float' around the values of adjacent channel(s). This is due to the high input impedance on the front end of the analog to digital converter and the inherent capacitance of the input stage. The capacitance charges up and holds the voltage since there is hardly any path for it to discharge into.
Thank you for that information. So how do i prevent this other channels' 'float' around the values of adjacent channel(s) ?.
-
Are your signals differential or (referenced) single ended, from what you describe, it sounds like your ground is not present and the card is going into its default noisy sine wave mode
I guess that too.
Today i tried what i got from the SCB 68 manuals for differial input. I connected a small 9V battery and place a 100ohms resistor acros a specified place on the PCB of the SCB 68. It was able to record the voltage as expected. However all the channels indicted values close to 9.1 V.
I expect only the channel with the battery to record this.
-
I am working on a sensor array- 6 sensors. I have connected the array through amp circuitry to SCB 68 box. I expect the MAX to give readings of sensor values. All i got was a noisy waveform on the MAX display. i used a multimeter to measure sensor outputs and detected an average of 1.5- 2 V, that was before a gain 2 amplification.
The readings on the sensor seem not to affect the reading of MAX test, as same reading continues after signals were disconnected.
What result should a MAX test panel give? Mine showed some continuously varying value until it stopped at around 10.8 V. I have just got DIAGNOSTIC Tool 2.0 to test the board and it indicated all is well: all PASSES.
What then may be wrong ?
Getting Labview to Aquire signals only an external swicth sends a
in LabVIEW General
Posted
Thank you for the helps i have recieved from this group.
I have this problem:
My sensors chamber unit have an external switch controling the solenoid valves which i must depress before i start data acquisition. I now want this switch to send a signal to start the LabView program itself to start, and to stop data aquisition after a timed interval.
My program VI is attached.
My intention is to use the loop on the left to recognise the arrival of the signal/ pulse from the switch, finish execution, pass control to the loop on the right.