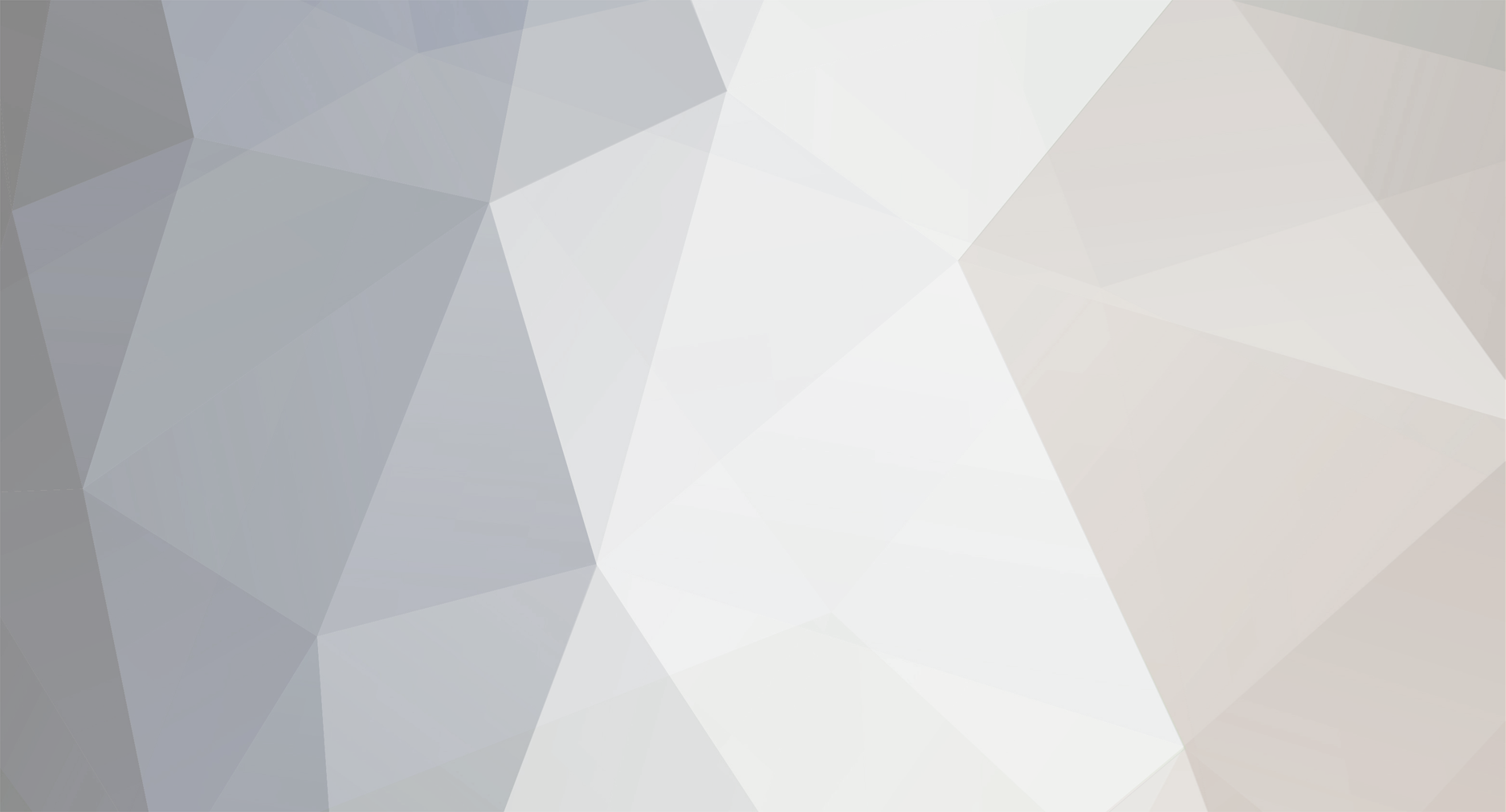
GraemeJ
Members-
Posts
36 -
Joined
-
Last visited
GraemeJ's Achievements
Newbie (1/14)
0
Reputation
-
Neither the tools palette or the controls palette are operating correctly on a machine running LV8.6 and XP. When a blank VI is opened and any simple program written, both the tools and controls palettes work correctly when using either auto tool selection or manual operation. However, once the file is closed or LV shut down, and then the file reopened, neither of the palettes operate correctly and further file editing cannot be performed. For example, with the tools palette and manual operation, the only tools that can be cycled thru are operate, breakpoint and probe while in auto the only tool is scroll. I have checked out this behaviour on four different simple programs and get the same response. The VI in all cases is unlocked. Any help in resolving this would be greatly appreciated. Regards, GraemeJ
-
An autosampler is being considered for future connection to a purpose built chemical analyser. The preferred autosampler uses a standard RS232 port. The autosampler manufacturer is mainly selling the RS232 version although also supplies USB, but in far fewer numbers. The analyser software is written in LV 8.6. No drivers exist for the autosampler. The intention was to use NI VISA and direct i/o to communicate with the autosampler, which will be located close to the computer. Data transfer rate will be low. Any advice or comments concerning reliability or any other issues on the following alternates would be appreciated. Output to computer COM port with direct cable connection to autosampler. Output to computer USB port and connect using NI Serial Hardware USB-232 1 port cable. Is this likely to give more reliable communication that 1. above? It would seem to have the advantage of using current technology, and also to use NI-Serial software to configure and monitor communication. Purchase a USB version autosampler. The sales history of mainly selling RS232 machines to OEM instrument manufactures left a small question mark. Not having a driver is unfortunate. The autosampler drivers on ni.com/idnet are not able to be modified since the details are not disclosed. I would be grateful if anyone knows of an open source version which I could use as a starting point. Regards, GraemeJ.
-
Thanks for the suggestion asbo. This would be easy to arrange. If bias resistors were in both the positive and negative leads of the amplifier output they would each have to be > = 125 K to satisfy the 250 K load requirement. This is only marginally greater than the range of 10 – 100 K that NI suggests for a differential connection in “Field Wiring and Noise Considerations for Analog Signals”. For a differential connection, the same document also allows a single resistor in the negative lead of a DC- coupled signal “required to satisfy the bias current path requirement” if the signal source impedance is “sufficiently low”. I could do with some help here – I do not know how to determine either value. A relay and single resistor solution would be great because the amplifier load is then the Daq impedance but, in addition, a lower value bias resistor, say 10 K, is the resistance between the sheath of the sensor and ground. Do you think that might be still a noise problem? The only other issue is possible noise from the relay. I had in mind a DIL packaged MOS relay. I would like to try and deal with (yet unknown) noise issues before the hardware is in the field (when it will be a pain to fix). Regards, GraemeJ.
-
An ion-selective electrode sensor, which gives a floating signal, is to be used with a USB6211 Daq. To reduce noise it would be desirable to use a differential connection but when the USB6211 is powered off, the problem below occurs. The only solution (?) I can see is to use very high value bias resistors but this means that the noise suppression sheath of the sensor cable has a very high resistance to AI GND. The sensor requires a very high input inpedance so the signal goes to a 1:1 gain amplifier with an input inpedance > 10^12 and the output is then connected to the Daq. However the amplifier, which is inside a Faraday Cage, is battery powered and permanently turned on, requires a minimum load of 250 K. The USB6211 has an impedance of 10 Gohm to AIGND, but when it is off the impedance is only 1200 ohm, and this becomes the load on the amplifier. The intention is to put a 130 K resistor in each of the signal lines to the Daq and use differential bias resistors of 270 K. This would become a voltage divider and reduce the magnitude of the signal but that is OK. However, it would also result in the sheath of the co-ax cable from the sensor having a resistance to AIGND of 130 + 270 K. I would appreciate any comments on a) the use of 270 K bias resistors, and b) the 400 K resistance between the sensor sheath and ground and its effect on noise suppression. Even more, I would appreciate any suggestions for a better solution than the above. Regards, GraemeJ.
-
External Hardware Pushbutton
GraemeJ replied to GraemeJ's topic in Application Design & Architecture
Thanks for the advise Daklu. It worked as you suggested but has now raised a further issue. The Exit button now no longer works because the DAQmx in th Wait case keeps running. If the external Stop button has not been pushed, I have not worked out how to detect this non-event and go to the Exit case The modified code is attached. Any further help you can offer would be appreciated. Regards, GraemeJ StopBtn - dynamic register5.vi -
The aim of the attached code was to respond to a pushbutton on an external piece of hardware. The VI is responding to the pushbutton action and lights the led on the front panel when the button is pressed. However, I cannot get the event in the Message Generator to respond to this, which also results in the Exit pushbutton on the front panel hanging up. Any advice would be appreciated. Regards, GraemeJ StopBtn - dynamic register3.vi
-
Is a low powered PWM controlled 12 VDC motor likely to cause interference with a DAQ board? The DAQ board, PWM controller and the motor will all be in close proximity in a small enclosure. The hardware details are: USB-6221 OEM (ie. no case) PWM controller: not selected, but typically operating up to 30 KHz. Motor 12 VDC 7 watt, geared brushed motor. The application is for speed control of a motor driving a peristaltic pump. Control of the motor requires it to run at two speeds: one at 12 volt, with the resultant speed not important (this is for purging the pump); and the second speed range, say at six volt, requires close speed control under varying load, with software speed control by the user. The varying load is due to the pump rollers progressively squashing the pump tubing. Any advice would be appreciated. Regards, GraemeJ
-
An update on my earlier post: I now have a current model external hard drive, complete with new “bells and whistles” user software. The good news is that this continuously and automatically backs up *.vi files, with up to 25 copies of earlier versions of the file. Setup was easy. If members thought it appropriate, I could post the make and model. Regards, GraemeJ
-
I have now found out that the manufacturers software can be by-passed so if the 'Bells and Whistles' version does not work, there is a fallback. Regards, GraemeJ
-
Thanks for all your replies. What should have been a straightforward exercise might be clouded by manufacturers backup software which is preloaded onto current external drives. My original question on the *.vi file extension was asked of (arguably) “the” major drive supplier. If it works as advertised, their backup software is a painless process for continuous and automatic backup. I guess it would be nice to have this but, if it becomes a problem, then the alternate is a bare-bones no-frills drive. Any comments? Regards, GraemeJ
-
I wish to automatically back up to an external hard drive and, in particular, back up *.vi files. Prior to purchasing a drive, in questioning a major manufacturer on the capability of their drive for different file extensions, the answer received was (quote): “Unfortunately, [ *.vi] that is file protected by copyright; the same laws that protect its contents, forbids us from using it. You could try to backup it, but it is not guaranteed to work without issues.” Has anyone any comments, or alternatively, suggestions of a currently available external hard drive that is OK for Labview files? Regards, GraemeJ
-
QUOTE (crelf @ Dec 20 2008, 02:07 AM) Sometimes this happens to my LV code - except it takes a bit longer to get the message.
-
QUOTE (normandinf @ Dec 17 2008, 12:49 PM) Thanks. Got lost trying to work this out.
-
QUOTE (normandinf @ Dec 17 2008, 04:10 AM) Is it possible to have a number of tab pages enabled simultaneouly, and then programmatically bring any one of then to the front? Regards, GraemeJ