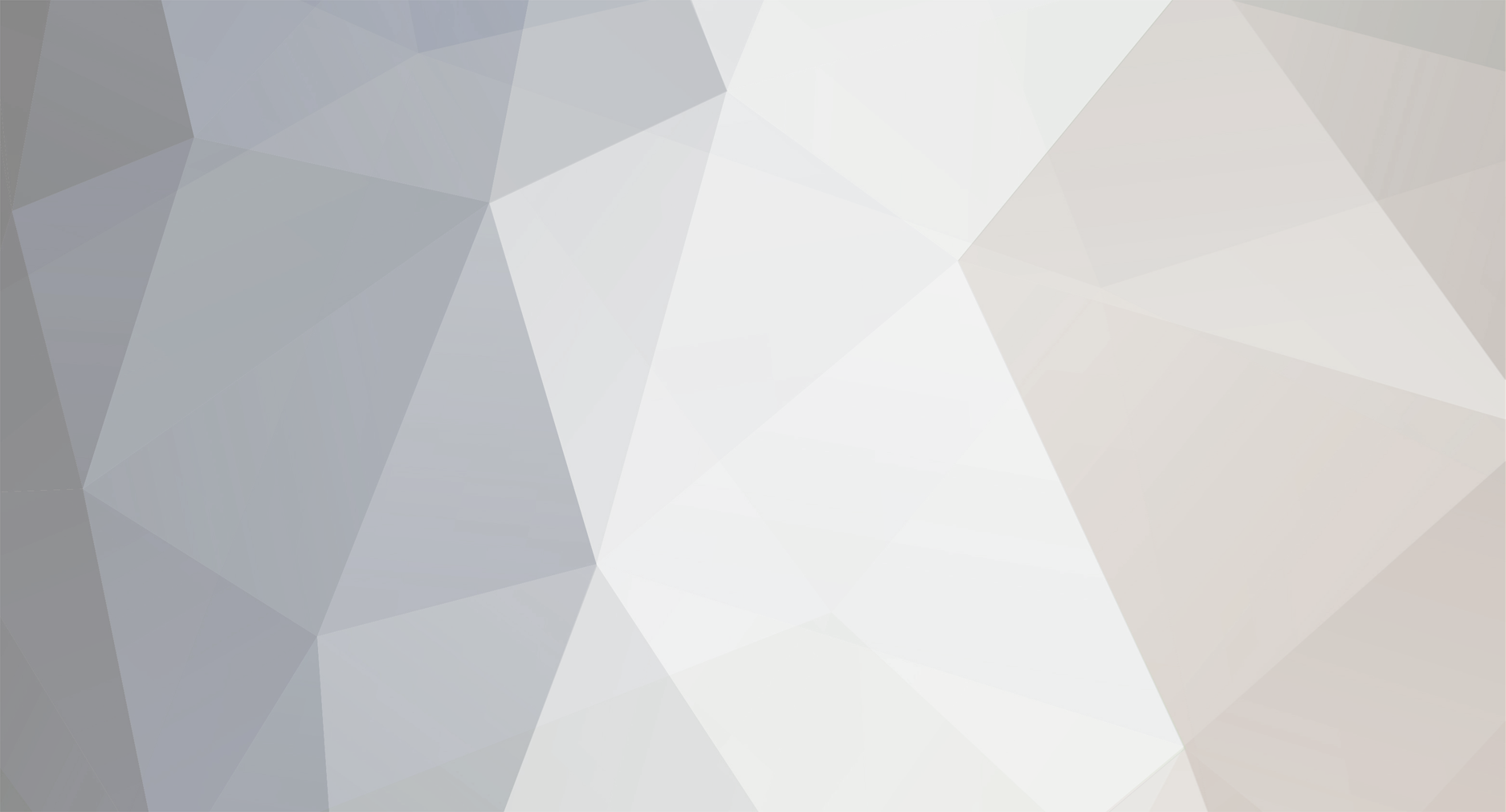
Michael_Burgess
Members-
Posts
27 -
Joined
-
Last visited
Never
Content Type
Profiles
Forums
Downloads
Gallery
Everything posted by Michael_Burgess
-
cheers dide only thing that i've noticed now is when I hit the stop button there's quite often a lag of about 4-5 seconds. Ideally it's meant to be an emergency stop - it halts all the parallel processes then the next part of the sequence writes zeros to all the ports to halt all activity. It was quick a while back, but now it's got a lag in it - down to those 'wait' functions you reckon?
-
which is better to use
Michael_Burgess replied to robert.berger's topic in Application Design & Architecture
I'm no pro by any means, but surely in any language you shouldn't pass around data you don't need to? I must say, since I discovered LV2 globals they're a godsend! -
sorted! pretty chuffed me thinks Download File:post-947-1112376890.zip
-
I'm assuming you mean along these sort of lines Michael? Only issue now is for some reason the output has stopped working in certain areas - if I do highlight execution things appear to happen - will my input VI cause issues do you think? The Chain Conveyor works, but the Sort Area is not firing the Solenoid - neither does the Assembly Area, but the Conveyor Area starts up the conveyor belt when it thinks there's both a peg and ring in the system (so this proves the Sort Area is correctly identifying them, just not firing the solenoid to sort the rings) and the Reject Area solenoid is firing too - so just seems to be the sort and assembly are playing up - odd - going to keep trying to work this out, but can you see anything that i've done in my labview naivety? My Logfile is all as it should be - so the SubVIs at least think they're doing what they should be - just the issue with the output - probably a schoolboy error on my part!!!! I've not changed the way that output writer works - odd! Can see a difference though - I've added a delay where I need it and the reject area solenoid still fires immediately when a reject object is in front of it - I'm just not too sure if my queues are working properly or not Any ideas dude? Cheers *EDIT* I seem to have sorted the problem by putting the index array functions for the input outside the while loop - that was the only difference between them and the reject area - thought I'd give it a shot - worked! When the index array was inside it seemed to look like it was iterating twice on the loop, so the outwriter value to fire the solenoid of '1' would be moved to the edge of the while loop, then it would iterate again, now the firing case was false, so a value of '0' overwrote the '1' waiting and then the loop seemed to release the new value of '0' to the outwriter, thus cancelling the original request to fire the solenoid! Weird! The only issue now is that sometimes if I halt the program with my Stop button I get an error from the 'pegqueue' or 'ringqueue' LV2 global I made saying there is a missing parameter - I think this is only when the queue is empty. *EDIT* Seem to have fixed the queue problem by turning off automatic error handling - although it's not ideal, handling errors is not really critical here - the hardware i'm working with has limited facilities in that respect *EDIT* put clusters in now to neaten it up slightly! Does my approach RE the queues look ok to you? You evidently know your stuff *EDIT* test tomorrow and I may well be done, give or take some frilly HCI extras long post anyone?
-
At present I've been using 4 queues to pass data around - 1 for identifying the peg number, 1 for the ring number, 1 for the first inspection area and 1 for the final inspection area. Is it still possible to use just 4 queues? If I obtain a queue outside of the parallel loops, then feed this into the six seperate loops, will the queues be passed around ok? I've got a feeling the queues won't run properly as one of the loops will effectively trap it until it finishes executing, which is when the program terminates? I've had trouble in the past with queues and multiple loops so not overly sure - going to back-up my work now and have a hack at it, but got a feeling it'll go pear shaped lol!
-
ah one more niggle i've seen when I profile the system using Michael's output method, it runs brilliantly - nice and quickly, lots of iterations and reacts more than quick enough to input in the assembly area though, I have to delay it somehow - basically when the sort area fires a plastic ring down the chute, if there's no already a plastic ring in the assembly hopper, open a solenoid to let this newly fired ring into the hopper - so firstly, I have to add a delay in the assembly area of about 300ms to let the ring slide down the chute before it opens - and I also have to add a delay of about 450ms before it shuts the solenoid so the ring drops down properly. this makes assembly perfect BUT completely slows down the program and reaction to input becomes slow generally - I can see from the profiling tool that the subsections iterate about 1/3 as quickly with these delays in - using the 'wait (ms)' node. hmmmmmmmm! if there a way to put a delay in without making the rest of the program suffer as a result? cheers
-
seems to be running pretty smoothly cheers Michael I've got a niggle with some Boolean Logic This attached VI basically picks up if a passing object is metal or plastic (assuming nothing of any other type has been placed on the conveyor) - I can do the metal identification easy, but for the plastic one I have a niggle - it works most of the time - but when the conveyor is moving quickly, it picks up the metal objects as both 'reject' (or plastic) and 'metal' So my code must nearly by right, just a slight issue in it - not really sure how to do a latch Boolean logic isn't my strong point - it's really bugging me!
-
well, top bloke! going to test drive that after the weekend but thank you very much for your help! RE the File I/O, it was still slightly iffy before I added that - I need to log everything that happens, in the order it does - I suppose a queue could do that, passing the queue to one subVI handling file I/O? Hmmmmm, that could work! I did wonder about the number of SubVIs - it seemed like it should be ok! thanks man
-
Ah Louis, what I thought may happen, has happened. Because i've got so many SubVIs and nested SubVIs (I need them really as i'm using Labview 2 style globals to manage counters and common repeating tasks - i'm assuming that's a good approach?) the performance suffers - now i've moved that into the main loop and removed the other, the output is occuring, but there's a lag and it's sometimes missing its deadlines. That was why I chose 2 loops - I might try and change the output to a queue maybe, to queue up all output, so nothing is missed - it's all a bit tricky!
-
That's actually a very good point Louis! I'm still adjusting to Labview, coming from a C programming background mainly, so the temptation to use local variables is far too great, when in actual fact the wire is labview's version of the local variable if i'm thinking along the right lines? I'm trying that out now! I can probably get my head round any timing niggles that occur this way! Fingers crossed - cheers
-
Just hit a new issue that I feared may rear its ugly head! If you look at Run.vi, you can see that each section in the bottom parallel process (while loop) passes an output value, which is then passed by local variable to the other parallel process (while loop), where it is output to the card. This output requires an 8-bit unsigned integer (the output port is 8-bit) between 0 and 15 (only the bottom 4 bits of the 8-bits are used, with values 8, 4, 2 & 1). I have identified the necessary binary value for each component (motor, solenoid etc) and this value being passed from each section will fire the necessary component when passed to the other parallel structure. The issue i'm now encountering, is that the top loop sometimes never gets the output value for the sporadic outputs, as the value I pass for output is part of a sequence diagram within a case structure (in the Assembly area for instance) and the sequence diagram executes so quickly, then the case becomes false and the output value will be set to 0 again for that section, meaning the top loop never received the output value. Can anyone think of an efficient way to ensure that any output I need definitely reaches the top loop? Bear in mind I need to output differing values constantly - it may just need 2 motors on at some point, then it will need to fire a solenoid, so it will still need to run the motors AND fire the new solenoid, then another solenoid may need activating at a similar time. Basically, a way to ensure that any 4-bit combination I need between 0 and 15 is output when I request it and it doesn't get overlooked. Cheers guys
-
Trapped Variable Problem
Michael_Burgess replied to Michael Aivaliotis's topic in Application Design & Architecture
in that attached image, the top loop which contains 'input' as a sub-VI doesn't appear to be working this subVI reads from port B, the input port I have tried putting input in a while loop to constantly read from the port, but the usual happens - as the loop is running, it will not release the input data to the notifier. I really am at the end of my tether with this - getting nowhere work mounting up - arggggggggggh! -
Trapped Variable Problem
Michael_Burgess replied to Michael Aivaliotis's topic in Application Design & Architecture
Cheers Michael, i'll have a read of that in the morning -
Trapped Variable Problem
Michael_Burgess replied to Michael Aivaliotis's topic in Application Design & Architecture
Hi Louis - thanks for that suggestion - I am attempting to use queues and notifiers. Basically, Port B on a 3x8-bit port interface card provides input. This is given as a figure between 0 and 255. Differing values = differing combination of sensors, so I need to pass the current input value to each section (I have identified 6 or 7 subsystems, each of which I will house in their own while loop) and act accordingly. I am using 2 queues to identify the number of pegs and rings in the system (the application is to control a production line simulation that sorts and assembles rings onto pegs and checks for correct assembly, rejecting the incorrect ones. I am also using a notifier to pass the Port B input value around the system. Here is a screenshot of what i've been working on tonight - I can't test it until I get into University tomorrow - best head to bed - it's 02:25 here in the UK! Cheers guys -
Trapped Variable Problem
Michael_Burgess replied to Michael Aivaliotis's topic in Application Design & Architecture
also just had this thought the input data will be changing very often - it could theoretically change a few times in a second I've just seen that there's a preview queue function, so I could theoretically have all loops preview the front of the queue and when they have done so, flag this, then have a loop that checks when all loops have checked the head and dequeue's the head if they have hmmmmmmmmm - a bit stuck here - I think queues may be too advanced for the problem at hand -
Trapped Variable Problem
Michael_Burgess replied to Michael Aivaliotis's topic in Application Design & Architecture
hey guys, knocked up a VI using a queue to get my head round them and must agree it's a very efficient way of handling large amounts of incoming data and passing them about however.................... I want multiple while loops to all read the same piece of data from the queue - so if I dequeue an element in one while loop and using another dequeue in another while loop, the second while loop will get a different set of data, the second in the queue - can anyone see a way round this please? I do like the idea of avoiding local variables at all costs cheers for your help guys -
Trapped Variable Problem
Michael_Burgess replied to Michael Aivaliotis's topic in Application Design & Architecture
cheers guys - going to look into it! any books to recommend to get down to the real nitty gritty in Labview? -
Trapped Variable Problem
Michael_Burgess replied to Michael Aivaliotis's topic in Application Design & Architecture
Hi Michael. what is a good way to pass data then? I'm still really new to Labview and always looking for new ways to work, providing it's within my capabilities! RE the event structure - I was trying to set it to react to the change in value of a boolean object on the front panel cheers -
Hi guys just a quickie.............. doing a piece of work in labview @ the moment............ got a problem i've encountered in the past and it's seriously annoying me! ok............. I have an 8-bit boolean array - i'm taking each bit and storing it into a boolean variable the actual variables themselves on the block diagram are elsewhere outside of this loop and i'm writing to a local variable from the 8-bit array so the bit from the array stores into the local variable no worries i have another local variable elsewhere on my VI in a differing while loop that reads the value of this and will react to a change in an event structure the local variable that is reading is not getting the value from the array, despite it storing into the local variable ok there in another while loop i was under the impression that local variables were a reliable way of getting info in and out of running loops? my tutor has suggested it may be thrashing, but my loops are all set with a uniform 'wait until next ms multiple' value in them - he also suggested it may be race conditions and i'm setting a differing value to this variable elsewhere, but there is only the variable itself and the 2 local variables related to which I have mentioned does anyone have any suggestions or things to try please? really stuck sorry my description is a bit poor, i'll knock up a small VI to illustrate what I mean when I get home shortly if necessary? cheers, Mike
-
Hi Louis. Thanks for your reply. What I sort of meant was that a loy of schemes i'm looking at now require or demand an engineering degree, even though I often fit the job 'desirables', let alone the pre-reqs. Was just a grumble on my part, as i'm looking forward to finishing education now. It's been 20 years pretty much (joined at 3, i'm now 23) and I really can't wait to get into my chosen career. Liking the idea of the states (without entering a whole argument/debate on politics, there's nothing keeping me here whatsoever other than immediate family) and am keen to see what's available. Cheers for replying Louis - just hoping there's a graduate scheme out there to satisfy my real-time interests! Cheers, Michael
-
thanks to both of you - seems like that may be what i'm after - if I build some functionality on top of that it should see me right - cheers
-
Hi guys, I'm due to graduate early summer with a BSc (Hons) Computing Science degree. In my final year i've specialised in Real-Time with 2 modules and a Real-Time final year project programming solution for a Bytronic production line simulation. I was wondering if you guys have any tips for companies to look at or apply to? I'm basically wishing to get a career rolling in Real-Time and would love to use Labview as part of my Job. I've applied to National Instrument's Graduate Engineering Scheme, but not heard anything back yet, although it's only been a week or so. One thing I do regret is not doing an Engineering Degree - it seems I may have found more applicable jobs easier with an Engineering degree under my belt - but alas, I am nearly complete with this course and I love what I do. I'm UK based, but I'm basically seeking work in the UK, US or Australia - the latter 2 will probably prove near on impossible to get into, but it's always worth a look I suppose! My CV is raring and ready to go, just got to start putting it out there now! Cheers guys
-
Serial Comms Issue
Michael_Burgess replied to Michael_Burgess's topic in Remote Control, Monitoring and the Internet
thanks for all the help on this guys I got 90% and am very chuffed! was worth 50% of a final year module! thanks! -
Hiya, Got an little issue i've spent a few days thinking about RE a programming solution - sort of getting there but got myself stuck on something. Basically, i've got an I/O card on a PC - which has 3 8-bit I/O ports. I have set Port A to output, Port B to input and Port C to output (Port C isn't really an issue right now). Basically, I want Port A's output to react to differing inputs on Port B. So, there's proximity sensors and other input devices on Port B. If need be they pass through an ADC, so all the Port B inputs are discrete binary values. The most significant bit on the port carries a value of 128, due to it being an 8-bit port, down to 1 for the most insignificant bit, and if all sensors were getting input the value would be 255, down to a value of zero when there's no input. I need to find a way of breaking down the input value (I am just presented with a single input value, say, 156 for example) and working out what sensors have been activated, enabling me to arrive at an output value for both ports A and C. That second part I have sorted in my head no sweat - just this issue with working out Port B's input is flummoxing me! The inputs I have grouped logically round the system - there's effectively 6 subsystems I have identified, although this shouldn't really make a difference to the method used to establish which sensors have been activated. Can anyone guide me at all please? I'm not very well up on how Labview can control binary as i'm still new(ish!) to it! I know I could probably do a binary look up table with a 256x8 array and then take the binary equivalent from the table, say, 11101011 for instance and from that work out which sensors have been activated and act accordingly? I know that a big array may be a lot of code, but it will be very quick to responde surely? This is going to be a real-time system, so reaction speed is key! Any help guys and it'd be much appreciated - cheers Michael
-
Serial Comms Issue
Michael_Burgess replied to Michael_Burgess's topic in Remote Control, Monitoring and the Internet
hey guys - thanks for the replies - what is this profiler? Will the help function explain it well? I do have delays on my loops - for the reason you stated - around the 150ms mark, just to stop labview thrashing away too much this is such a hard assignment lol! Louis - i'm fairly sure what you said is the issue - labview is thrashing away at the port but it seems to take a computing age for things to get through if you have any tips it'd be much appreciated cheers the assignment is using 2 PCs - bit daft - I have 2 so can do it at home, but most people won't and means they'll need access to uni over xmas instead of going home! cheers guys