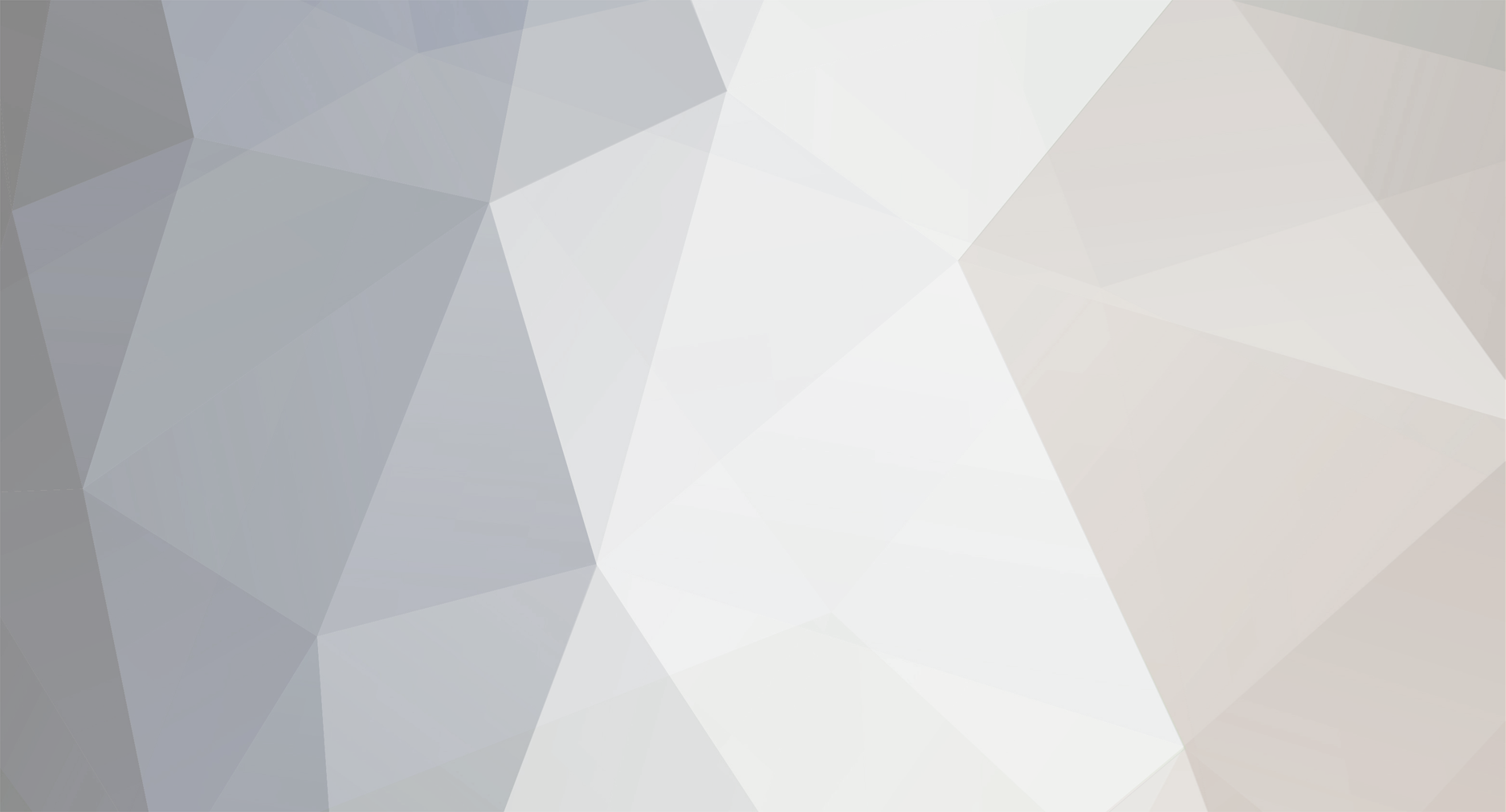
bono02
Members-
Posts
22 -
Joined
-
Last visited
bono02's Achievements
Newbie (1/14)
0
Reputation
-
QUOTE (Ton @ Nov 2 2008, 01:12 AM) Hi Ton, Thank you for your reply. However, I could not find example in ni.com related to auto-initialize function. Could you give me one example? Or perhaps what you meant was the create instance function (like constructer in C++) in LV Object Oriented Graphical Programming, was this what you mean? QUOTE (Ton @ Nov 2 2008, 01:12 AM) However I advice you to timed IO within DAQmx, so the timing is handled by the daqmx driver and not by LabVIEW. To do this you should create a clock on your 6259 of 5 ms, and do a burst read in LabVIEW of 1 sample, no timing needed the speed will be limited by the DAQ card. Did you mean using external trigger? I am not planning to use ext. trigger though, since I desire only to use the source from a single machine.
-
This is a cross posting, I also posted in here: http://forums.ni.com/ni/board/message?boar...;thread.id=4915 I hope others LaVa's member could help me faster... ----------------- Hi all, I am using LV RT8.5 with 2 PXI installed, the PXI-7358 and DAQmx PXI-6259. I wrote a program in LabView RT of a single timed loop with time constraint 5 ms. The first program, the loop rate was OK (no delay, finished late boolean is false), however, when I added a subVi, suddenly the loop rate became high and delay occured (finished late boolean is true).The delay could reach to 100ms I attached the pictures below. 1. The fine loop without subVi 2. The loop with subVi 3. The subVi What I guess now the problem is because of the DAQmx create virtual channel and DAQmx start. However, If I remove these functions from the subVi, thus I have to connect the DAQmx create virtual channel and DAQmx start in every main program, and thus it will give so much work and make the program more complex. Are there any solutions for this. I really appreciate your help. Regards, Bondhan
-
Hi all, I am not sure if I put my question in the right forum. Anyway, I have a question. I am planning to use the measurement studio using Visual C++. Has anyone ever tried to access shared variable from the measurement studio using VC++? I tried to find in the google, but I can not find the examples. Thank you.
-
QUOTE(ashishuttarwar @ Jan 17 2008, 02:16 AM) :thumbup: I was not telling matlab is better than LabView . Well, in my experience I am coming from asm, C, C++, Matlab then to LabView, though I use several of them at the same time. Anyway, jbelim goodluck for your project. I think Lavag members will kindly help you, as they helped me many times :thumbup:
-
QUOTE(jbelim @ Jan 16 2008, 11:00 AM) Hi Jbelim, I now this is LabVIEW forum. Why do you choose labview? Have you tried matlab. AFAIK, Matlab is a good choice for theory processing esp. image processing. Also IMO, LabView is more close to real application (GUI) and hardware interface.
-
Coding Technique and Motion Controller
bono02 replied to bono02's topic in Application Design & Architecture
QUOTE(bono02 @ Jan 1 2008, 04:05 PM) The problem is solved. In case anyone has similar question, the answer is in http://forums.ni.com/ni/board/message?board.id=240&message.id=5813#M5813' target="_blank">here. -
QUOTE(venkatesh @ Dec 31 2007, 06:38 PM) When we were in high school we have this equation Theta = Amplitude * Sin (2*Freq*Time), here, you can define the time/period and amplitude. If you want to get the speed you can differentiate, also for acceleration. Hope it helps.
-
Hi all, I have several problems here, I tried to google but still I could not solve the problem. Here are my questions: 1. I tried to download an example program of EPOS which require to download a DLL file into the RT, but it failed, here's the error (I attached the picture) 01/02/2008 13:29:50.511 [error] LabVIEW: Failed to load shared library EposCmd.dll:_VCS_GetProtocolStackName@16:C on RT target device. From the NI.com forum, I found a similar problem and it said by installing Network Variable Engine and Variable Client Support into the LV-RT, and I did, but still failed. Any one can help me about this? 2. I posted a question also in lavag, I think this section is more appropriate. "I am trying to use the digital IO of the motion controller of 7358, but then I realized the delay is more that 1 ms (I checked using the oscilloscope), I attached the code (MOMO = Must On Must Off). Is this real, I mean the hardware delay between on-off is as big as this? Anyone knows the solution for this?" Note: I am using LV-RT 8.5, PXI-7358 Motion Controller, EPOS 70/10 Thank you for any help
-
Coding Technique and Motion Controller
bono02 replied to bono02's topic in Application Design & Architecture
QUOTE(bono02 @ Dec 31 2007, 10:01 PM) Hi all, I answered my 2nd questions, It is caused by the glitches (see the picture from my previous post). If we use the DAC vi independent from motion axis, we HAVE to disable that axis so that it won't glitch. Now about the 1st question, any answer? Thx. -
Coding Technique and Motion Controller
bono02 replied to bono02's topic in Application Design & Architecture
Hi all, it's me again, don't get bored . For martin thank you for your reply, I already quite finish the contour movement. I realized that the update rate is the time between two points (Thus we can measure the time for the whole trajectory). For somehow if we set the point too far between two points and the update rate can is beyond the speed, then the motor cannot follow the points given. Now the problem is the speed is too slow (though I am using 10 ms), I am thinking of changing the trajectory. Anyway, I have several problems: 1. I am trying to use the digital IO of the motion controller of 7358, but then I realized the delay is more that 1 ms (I checked using the oscilloscope), I attached the code (MOMO = Must On Must Off). Is this real, I mean the hardware delay between on-of is as big as this? Anyone knows the solution for this? 2. I am using DAC (I attached the code), I read on the oscilloscope that the signal is not really what I want (I think because of the sampling, I attached the oscilloscope output picture). On the oscilloscope it is read that the amplitude is for 10 V, but in multimeter it is only 2 V (I think because the multimeter measured the RMS value). How to generate a real RMS value using DAC in motion controller? All of this code is downloaded into the LV-RT 8.5 Thank you -
Coding Technique and Motion Controller
bono02 replied to bono02's topic in Application Design & Architecture
Hi martin, Thank you for your answer. I tried several times, but the motor only moved a bit. I tried these steps (stepper motor) with absolute contouring: 1000 2000 3000 4000 5000 with velocity 137795 steps/rev equal to 13 RPS I don't know why. I think this is the fastest speed of the motor, because if you increase the speed the motor will not move anymore. I read in the manual that "no consecutive points can differ by more than 2^15-1", and my steps are just fine, and also it said that the data in-between two points will be spline-interpolated. Is it possible to have a position (a b c d e..n) and then just by giving the time from a to n (with the velocity is derived automatically)? Btw, about the maxon motor, are you using the API provided or you directly drive it using motion controller? Here with me I have EPOS 70/10 and Maxon motor EC 45. Thank you. Bondhan QUOTE(martin@aerodynamics @ Nov 28 2007, 12:26 AM) -
QUOTE(Daklu @ Nov 22 2007, 04:59 AM) "We don't want people to create block diagrams more than one screen size." I agree with you, zooming would be better. It's painful by dragging the slider right and bottom, also by using navigation window, we still have to click on that small window, a shortcut would be better! For writing comment I usually did shift+right click, and choose the Text icon (I think this is a standard one), why do you need string constant? Also the front panel, sometimes in the Back Panel I create a ctrl or indicator, then when I switch to FP, I have to -again- drag the slider to find the control/indicator which has been created And another one, for XP user maybe you can consider of installing a free add-on from Windows, http://www.microsoft.com/windowsxp/downloads/powertoys/xppowertoys.mspx' target="_blank">Powertoy the alt-tab replacement, you can click on the small-screen when you are switching window using alt-tab. Bondhan ~Another Certified LabView Newbie
-
Coding Technique and Motion Controller
bono02 replied to bono02's topic in Application Design & Architecture
QUOTE(martin@aerodynamics @ Nov 20 2007, 08:11 PM) Hi Martin, I need another help. I tried to find a contour move with different speed configuration in ni.com, but I could not find any. Is it possible to have different speed for different position in countour move? Do you have example for this? Thank you. Bondhan -
Coding Technique and Motion Controller
bono02 replied to bono02's topic in Application Design & Architecture
QUOTE(martin@aerodynamics @ Nov 20 2007, 08:11 PM) Hi Martin, I need another help. I tried to find a contour move with different speed configuration in ni.com, but I could not find any. Is it possible to have different speed for different position in countour move? Do you have example for this? Thank you. Bondhan -
Coding Technique and Motion Controller
bono02 replied to bono02's topic in Application Design & Architecture
QUOTE(martin@aerodynamics @ Nov 20 2007, 08:11 PM) Hi, Can you explain why the MC will multiply with 4? Where can I get this information? in which manual? Btw, the encoder is going to be used for servo motor. For the stepper I have potentiometer feedback. Thx