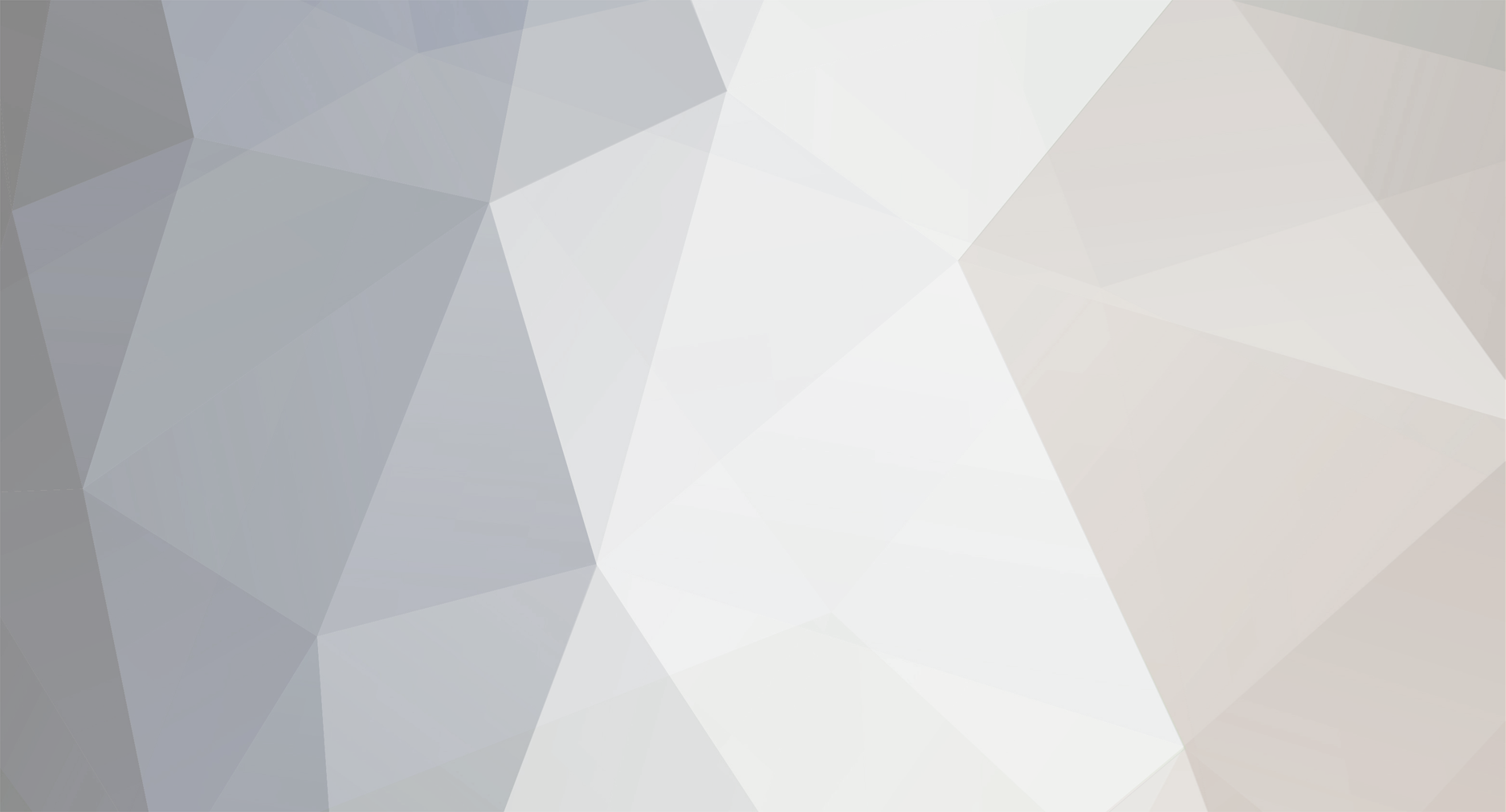
Tim_S
-
Posts
873 -
Joined
-
Last visited
-
Days Won
17
Content Type
Profiles
Forums
Downloads
Gallery
Posts posted by Tim_S
-
-
-
QUOTE (sukhiray @ Sep 10 2008, 02:59 AM)
1. I have to change the time axis into deg. the relation b/w these two is like thatdeg. value, say, D=t*5000*75 t is in sec.
and then have to plot the signal against this D
There's not really enough information to help you with your third item. You can find examples for your second item (interfacing with Excel).
For the first item, you seem to have a formula (though I don't understand your constants) to convert the dt into a delta-angle (d-Theta). I assume you're using a waveform, so all you'd need to do for the plot is to replace dt with the new value and ignore the timestamp in any plot.
Tim
-
QUOTE (dangan @ Sep 3 2008, 04:02 AM)
Hi everybody, I am researching to labview. If I want connect between labview control and capture system on computer, how can I do?. I want use Labview control probe of ultrasound on Ultrasound machine.Thank youYour question needs some more detail to provide an answer. LabVIEW supports many communication protocols for talking to external devices including serial, TCP, CAN, ProfiBUS, and DeviceNet. LabVIEW supports ActiveX, .NET and DLL calls for interfacing with code on the same computer. This provides a huge range of options to where, to date, the only code that I'm personally not been able to communicate with was never seriously updated from a DOS application.
Tim
-
QUOTE (manikanth @ Sep 2 2008, 02:29 AM)
m making a simple project i.e to control a simple electronic circuit.only on and off functions should be done from the systemplease somebody help me.................
You haven't listed what hardware you are using to perform the control. Is this a NI DIO card? Parallel port bit? Ethernet device? I assume you are using a DIO card, in which case I recommend looking at the example code that ships with LabVIEW; there are digital output examples that ship with LabVIEW.
Tim
-
QUOTE (b_subhasis @ Sep 2 2008, 02:11 AM)
I had a requirement to convert a html file to a pdf using a VI.I have tried finding the web for a solution or an idea.But could not find any.Has anyone got an example to convert the same.Are you converting the code to write a pdf instead of html or converting the existing html to a pdf? I assume the second... It seems the easiest option would be to install a pdf writer (looks like a printer) and then print the html from a web browser, which could be controlled programically using ActiveX or .NET.
Tim
-
QUOTE (JohnRH @ Aug 28 2008, 07:34 PM)
QUOTE (JohnRH @ Aug 28 2008, 07:34 PM)
What would be really cool is something in which I could activly link the blocks to the lower level design detail. (circuit diagrams, interface specs, LabVIEW FPGA code, LabVIEW software, etc.)My previous employer didn't have anything (well, Paintbrush) available to me, so I faxed hand-drawn diagrams to the electrician/drafter/electrical designer/jack-of-many-trades. My current employer has AutoCAD; I'm finding that's overkill, but it does allow for a lot of text to be put into place and the diagrams can be included in the prints or drawing package. Most of my diagrams are stored as digital pictures of whiteboards, though.
Tim
-
QUOTE (TobyD @ Aug 27 2008, 07:16 PM)
I'm curious what people think of the Automatic error handling options in LabVIEW. Is this something you leave enabled? Do you disable it? Why?Automatic error handling has been one of the options I turn off once LabVIEW is installed. The why is it would report errors and wait for a user prompt when the systems I work with do not have a user standing in front of them (it's mostly production equipment).
QUOTE
This brings up something I am really interstied to learn. How do other people do their error handeling?We have a centralized alarms screen that logs to a database.
-
QUOTE (Dev @ Aug 21 2008, 11:55 AM)
I m using a dual axis accelerometer adxl203 to measure collision.I am able to detect them but i need some help as to how to count/store them whenever i see a spike(which indiactes there has been a collision).I tried using a peak detector but finding it hard to count them.Any suggestion is appreciated.Can you post a snapshot of what you're trying to analyze? It's difficult to provide suggestions otherwise.
I would expect that a simple threshold crossing would be able to detect the peaks you're looking for.
Tim
-
QUOTE (Tom Bress @ Aug 21 2008, 09:59 AM)
I think you have that last part backwards. The first exam is very broad, and all engineers in all disciplines take the same test. The second exam (the blue book written test) is in your discipline. For example, when I took the second exam it was specifically in the field of mechanical engineering.Quite possibly as my information on Michigan PE exam comes from my father, who last took it in... 1972, I think. He did mention that each state has it's own test, rules and regulations.
-
QUOTE (crelf @ Aug 20 2008, 04:14 PM)
what does a Professional Engineer certification really mean?There are federal regulations in certain industries (like power generation) requiring you have to have a PE sign off on any design before it can be implemented (I think this also impacts contracted work). This provides some protection for the company as the PE takes some liability for the design in that it will work and it will not negatively impact other systems (as in moving this thermostat will not impact the safety systems keeping the power plant from blowing up... seriously). A PE that signs off on bad designs will shortly be out of work with, at best, a bad employer reference. To pass the PE, you have to show broad knowledge beyond your field. The first part of the exam is in your field; the second part occurs years later and cannot be in your field.
-
QUOTE (martin zhxie @ Aug 19 2008, 03:51 PM)
I am new to labview. Currently I am doing a automation romote control to a testing system through TCP/IP. The communication from teststand to labview has been done by using queue. It outputs some data. Now I need to pass these data back to teststand and do some caculation to them. Then loop them back to labview.You may want to look in the Code Repository and on NI's website. There are network communication schemes such as the Publish/Subscribe (http://forums.lavag.org/Publish-Subscribe-file122.html). I also recall running across a networked queue, but can't seem to locate where that was.
Tim
-
QUOTE (BrokenArrow @ Aug 7 2008, 10:47 PM)
I think I have an issue with VISTA and LabVIEW, where I start LabVIEW and the CPU jumps to 50 to 60%, and when I quit LV, the CPU stays high until I restart the puter. Any thoughts?Version 8.5.1 and Vista Homer Premium 32-bit.
I'm not running Vista, but...
Have you looked at the processes tab of the task manager to see who's using the CPU? The type of behavior you're describing can happen when a program becomes a zombie (I've had some of my LabVIEW programs do this under NT and XP.). Usually I see LabVIEW still listed under the Processes tab of the task manager but not the applications tab when this happens.
Tim
-
QUOTE (Dan Bookwalter @ Aug 7 2008, 11:39 AM)
When you wrote shaker I was thinking of something like http://www.bksv.com/doc/bp2101.pdf, which is quite a bit smaller. What you have seems like a guaranteed noise source, though I would think that it would be more at a fixed frequencies. You could get broad-spectrum noise if the shaker uses a variable frequency drive and the drive is attempting to hold position. (We have this problem with synchronous AC motors.)
-
QUOTE (Dan Bookwalter @ Aug 6 2008, 01:42 PM)
How are other people doing this stuff ??p.s. the DAQ card is a PCI-6071
We've used accelerometers, high-bandwidth torque transducers and (played with) laser vibrometers connected to a NI PCI-4472 card and an 18-bit M-series card (I don't recall the number). We were using a 6071E, but the NVH expert we hired laughed the board out of our NVH use; 16-bits is the bare minimum if you have everything perfect and 20 to 24-bits is prefered. The 4472 is nice in that it has anti-aliasing filters on-board.
You mentioned that you're connecting your grounds together... that may be causing problems if you're creating a ground loop. 50 mV of noise would be 10-bits for a 12-bit card... that's not a lot and could be induced by lots of things; what frequency is the noise at and what could be causing that? You mentioned that you are using shielded cable; are you using twisted pair? Are the shields connected at only one end? No ends? Both ends? Shields should be connectedat one end and carry through for low frequency signals, but the rules change when you get to mid and high frequencies. High frequency noise should have the shield connected at both ends. Mid frequency noise can require both, one, or neither end of the shield to be connected. Then you get into conncting caps between shield and ground and it gets to be a mess. I'm not sure how to help more without knowing more about the hardware.
Tim
-
QUOTE (Xrockyman @ Aug 6 2008, 11:22 AM)
In the front panel control menu there is a control "File Path Control", with this I can get a path to specific file. What I want is the same thing but only to folder. I don't want to open a file I only to choose a path.The properties of the control allows you to change the "Browse Options".
-
QUOTE (alukindo @ Jul 31 2008, 12:00 AM)
. . . . Any thoughts on how to get the picture control to output clean/sharp PDF or printed images of itself?I recall running across a 3rd party purchasable module for LabVIEW that would let you write PDF's. Unfortunately, I don't recall where I found it or what it was called at the moment. Sorry that I don't have more information at the moment.
As for printing the picture control, I assume you're converting the picture data to a bmp, jpg or similar for printing. You may be seeing the resolution of the picture control; is there a way to make the picture control larger and then print more dpi? You may also be seeing the result of conversion to a lossy file format (which jpg is).
I expect your code is huge to produce that image. Can you post your printing routine?
Tim
-
-
-
QUOTE (urh8 @ Jul 22 2008, 06:33 AM)
it seems like there is a strong noise source on the output.When i watch my output in labview it looks perfect but on the osciloscope i can barely recognize the signal.I would recommend two things:
1) Disconnect everything you can and connect only the oscilloscope to the analog output.
2) Disconnect the oscilloscope from ground.
The second can be very important. There are some oscilloscopes that can create a ground loop through the ground pin of the power plug -- at least with US-style three-prong plugs. I assume that other styles of plugs can also create this issue.
-
QUOTE (Götz Becker @ Jul 16 2008, 03:20 AM)
I guess I didn´t take enough time to write me question in the first place. First my in case I doesn´t use indicators inside structures, just a control.I am just not sure if and why LV would optimize the lower solution better. It´s not that important just something I wondered about
My understanding is that reading a control or setting an indicator switches to the UI thread. I would guess that the lower is more optimized because all of the controls are read at the same time, thus only requiring a switch to the UI thread once.
Tim
-
QUOTE (sisson @ Jul 14 2008, 01:53 PM)
In my connect function , i have wired a username, password, and the udl file as inputs. Strangely, every so often (usually when i reboot the computer or wait about a half hour), i will get an error with the code "-2147287038" which isnt documented in the error codes library.Try an internet search for mySQL and 2147287038. There appear to be over 700 results when I tried. Remember that putting the - sign in there will eliminate results that have a 2147287038 in them.
Tim
-
QUOTE (ikos74 @ Jul 10 2008, 12:10 PM)
There is a .NET class library if you go to the driver section of the Advantech website. LabVIEW can interact with .NET objects.
Tim
-
Hi!
in LAVA Lounge
QUOTE (electrika @ Jul 9 2008, 03:01 PM)
I am trying to write the data generated by labview to an excel file. The thing is that I have two sources of data and I want to write the data from each source to two different columns of the same excel sheet. Since I am not very well versed with labview I am not sure if this is possible. How can i do this?Yes, it is possible.
However... you may wish to use a CSV file, which is fully compatible with Excel; this would be much easier to implement. This would involve opening a text file and writing out any header, then write out your values. CSV is pretty widely known and documented, so I won't go into that.
Tim
-
QUOTE (Phil Duncan @ Jul 9 2008, 12:16 AM)
Taking a quick look at the data sheet for the sensor, it appears to go down to 0 Hz, meaning you can measure a static load, however there is attenuation of -5% at 0.0003 Hz (effectively 0 Hz). You mentioned AC coupling... that will take out any static/DC signal you have; switching the settings to DC coupled will electrically allow you to measure a static load. I'm not familiar with the SCXI module to help you there.
Hope that helps.
Tim
How to create a settings page similar to MAX
in Hardware
Posted
QUOTE (dblk22vball @ Nov 21 2008, 11:15 AM)
[snip]
I think you can get the look you're seeking with the tab control. The tab control can be made invisible and the tabs hidden.
I've used subpanels for similar functionality and it's a bit of a pain handling when the user clicks on the "ok" button as it was not very clean to handle saves, especially when an error occurs. I'm certain there's better methods than what I used (hidden boolean on the subpanel), but everything we were coming up with required a fair amount of time we didn't have.
Now, should you have a dynamic list of configuration options (say from plugins), then I expect you'd need to use the subpanel to get the look you're going for.
Tim